4 minute read • published in partnership with Cimlogic
Insight: Sustainable manufacturing – more than just a buzzword
A quick perusal on the websites of any of the biggest names in food & beverage and life sciences companies and we inadvertently stumble upon the corporate commitment to sustainability. The goals are similar: the decoupling of growth from the environmental footprint, and increasing social impact. Promoting ethical behaviour is good for a brand and ultimately helps to boost sales. Business growth is great for employees and shareholders alike but should not be at the expense of the planet. Cimlogic explores the steps manufacturers can take to embrace sustainability.
So, what about manufacturing? This is the creation of manufactured products through economically sound processes that minimise or eliminate negative environmental impacts whilst conserving energy and natural resources. Many of the practices we see today in sustainable manufacturing have evolved from lean manufacturing and efficiency improvements. Eliminating downtime, reducing scrap, improving traceability, improving quality, and increasing automation all point toward increased profitability. Reducing energy consumption (Water, Air, Gas, Electricity and Steam, or WAGES) is one of the historic drivers, with the UK government offering manufacturing organisations financial incentives for doing so. After all, it is estimated that manufacturing operations used somewhere in the region of 20% of UK energy consumption in 2020.
We are making great progress so far. Engineers happen to be natural problem solvers and come up with ideas every day with new ways to conserve energy, reduce waste, and eliminate pollution. All with the end goal of manufacturing products in sustainable ways. The current climate of achieving these environmental and economic goals is proving to be a challenge that the team at Cimlogic love to deal with.
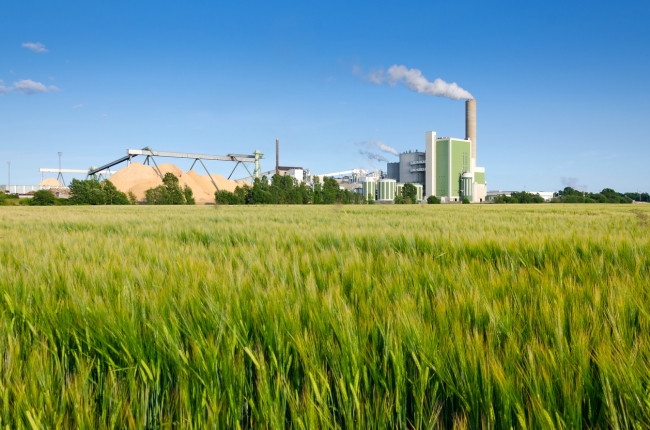
Sustainable manufacturing is a mindset rather than a series of steps – there are steps that can be taken when thinking towards sustainable manufacturing / Picture: Getty/iStock
Let’s take a look at some different initiatives in making manufacturing more sustainable.
Reduce waste
How do we consume just the right amount of ingredients and resources to produce high-quality finished goods? Historically we saw a focus on getting products to market in as short a time as possible and reducing production costs. What we didn’t see was consideration for the resources we were using. Excessive use of paper, metal, and packaging materials. There have always been ways of reworking waste materials, but that comes at a cost. Instead, we need to weigh up the investment in precision manufacturing equipment and processes that minimise raw material use from the outset.
Cut Down on Fossil Fuel Usage
Whilst it may seem obvious, reducing or reaching net-zero energy spend is a win-win nowadays. With half of the world’s reserves used up, and oil supplies well beyond peak, there is no reason not to reduce consumption of these precious resources. Alternative energy sources such as wind, solar and sustainable fuels are still in development and not yet an economically viable alternative. However, there are other ways to drive down energy consumption. Using predictive techniques to determine the optimal time to replace any components that may lead to poor machine performance. Using variable speed and servo drives in place of single speed or direct drive motors, generators and pumps.
Recycle, Recycle, Recycle
We can’t always reduce the amount of waste material in a given process. We can however reduce the energy consumption in the transport and processing of the waste materials. Rather than fill containers with excess material, waiting for it to be taken away for reprocessing we can look at ways to compress the waste into more manageable shapes. These take up less space, are easier to transport, and use less energy overall. Taking this to the next step, companies are now investing in equipment to process waste materials on site, ready for almost immediate-use.
Embrace Digital Technology
The 4th industrial revolution has been with us for a number of years now – the merger of Automation, IoT (the Internet of Things), Artificial Intelligence, Big Data, and Cloud Computing. We have touched upon this subject, albeit briefly. The ability to create digital twins and carry out endless modelling of various process improvements provides a way to accelerate manufacturing efficiency. When combined with the latest advances in robotics and autonomous vehicle technology we are able to drastically reduce human error, the need to work in harsh environments or carry out repetitive tasks by hand.
The list is endless. Above are just a few steps that can be taken when thinking towards sustainable manufacturing. Many of them do require an upfront investment, but the majority of this can be recouped in 5-10 years when taking into account the increases in efficiency. Sustainable manufacturing is a mindset rather than a series of steps.