3 minute read • published in partnership with ABGI
Insight: The results of innovation in manufacturing and boosting business growth – part 3
At a time when businesses across the UK are grappling with unprecedented challenges, access to funding to increase cashflow and help mitigate the disruption has become a top priority. There is no doubt that British companies which have been involved in R&D and those which turn out to be hugely successful are linked. In this series of articles, we share with you case studies and practical examples of manufacturing businesses that were able to claim funding on projects aimed at improving products for market by making them cheaper, faster, smaller, larger or more efficient. In the third of a series of articles, ABGI looks at how innovation and R&D in the manufacturing sector can ‘make things stronger’.
Part 3 – Does strong only ever just mean strong?
When we talk about making things stronger, we often think that the end result is that they will be “sturdy”. This might not be strictly accurate. Often the same technical challenges are faced in making products or components more durable or in reducing the impact of wear & tear. Especially when we are trying to extend the life expectancy of equipment developed for harsh environments, improving resistance to corrosion or extremes in temperature.
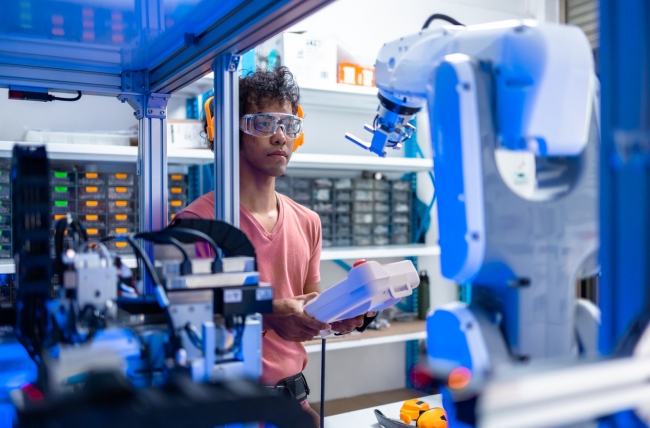
ABGI is encouraging manufacturers to look at process improvement opportunities that could help boost business growth / Picture: Getty/iStock
Graphene is the new black
At its simplest level this will include experimentation around how to most effectively incorporate new materials, that are known to add strength to a product, or remaking products entirely from new materials. Currently there is a considerable amount of research and development around the incorporation of graphene in products. While graphene is both very strong and flexible it is also particularly expensive and the challenge is currently to find the most cost effective approach to imbue products with the strength of graphene without making them prohibitively expensive, such as trying to combine graphene in the sole of running shoes strengthening the sole but still keeping them within the budget of the average runner.
Fly me to the moon (in a light and sturdy aircraft)
Over the last ten years the development of new alloys for advanced manufacturing has been gathering pace, such as the use of an aluminium-lithium alloy in the manufacture of aircraft fuselage. This new alloy offers improved stiffness, better corrosion resistance, improved fatigue strength and all with a significant weight saving on aircraft using traditional aluminium alloys or fibre composites. However, this innovative material solution was not a simple make it and use it. There has been on-going research and development over years to identify the Al-Li alloy providing the most appropriate mix of characteristics, not to mention endless prototyping and testing to ensure that this was in fact the best material for individual components.
Additive manufacturing to the rescue
For one moment let’s turn our attention away from traditional manufacturing to construction. Pressures on the sector to reduce 1) costs, 2) on-site health & safety risks and 3) environmental impact have driven companies to invest significant resource and effort into R&D around new materials and civil engineering. Their aim is to create lightweight building systems that provide load-bearing capacity with structural integrity, whilst offering environmental credentials (either using recycled materials or allowing increased recyclability of the finished product).
The quest for stronger, more robust products and designs has been given a serious leg-up through the development of additive manufacturing. While we don’t have the time here to discuss the finer differences between vat photopolymerisation and binder jetting or sintering, it is worthwhile noting that additive manufacturing has allowed designers and engineers to experiment with forming processes in producing more intricate parts with fewer seams or joints, thus enhancing the structural integrity, robustness and strength of products. If only it were that simple! Additive manufacturing is still in its infancy and like all new technologies still needs to be developed and perfected. There is still considerable research and development required around the substrates being used and how best to utilise them in the new forming processes as well as the binding of compounds and in curing processes.
The great news is that much of the development necessary to create materials that are stronger, sturdier, more resistant and durable work is still in uncharted waters and as such will provide adequate grounds for R&D tax relief and in some instances may also provide patentable intellectual property and potential Patent Box relief throughout the commercialisation of the technology. This could net the companies behind our “tougher than the rest” materials significant funding to inject back into their business, and accelerate future innovation and business growth.