8 minute read • published in partnership with Evocon
Insight: The top 8 OEE calculation mistakes
Implementing OEE can significantly improve productivity and open the door to great opportunities for your organisation. On the other hand, making mistakes in the OEE calculation can ruin the expected outcome pretty quickly. To base your decisions on accurate data and conduct meaningful analysis Evocon explores the 8 top OEE calculation mistakes organisations tend to make when calculating OEE what to do instead.
1 – Not paying enough attention to all production stops
In manufacturing, reasons for stops are defined either as “planned” or “unplanned”. Planned stops, also known as “positive stops”, consist of changeovers, setup time, cleaning and scheduled breaks such as lunchtime, amongst others. Regarding planned stops and OEE calculation, there is one very common mistake organisations tend to make.
When evaluating the stops in the production process, companies consider many of them to be “planned”. So, they do not pay enough attention to them. Most managers see the time spent on these stops as necessary, whereas in fact it can be optimised.
As a result, due to not evaluating the reasons for the stops properly, production teams may miss the opportunity for growth and improvement on the shop floor.
What to do: As an essential part of the production process, planned reasons for stops can present opportunities to improve production when included in the OEE calculation. Therefore, it is crucial for organisations to analyse each reason. They need to see the bottleneck behind them, rather than simply counting them as planned stops.
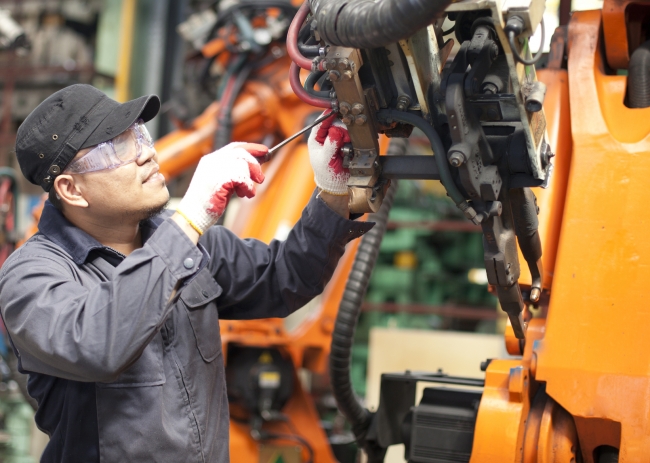
Implementing OEE can significantly improve productivity and support growth opportunities / Picture: Getty/iStock
Production downtime can hide some technical and operational problems within the organisation. Maybe there is a machine-related issue that makes your team lose time (and money). Furthermore, this issue requires maintenance as soon as possible. Or your production manager may need to arrange the changeover times more effectively to make the process flow better.
Taking all the reasons for production stops into consideration helps you see how and why they affect your productivity. Thus, you can come up with solutions to optimise your processes more efficiently.
2 – Excluding operators from the OEE implementation process
Operators are on the frontline of your production team. They play a key role in driving efficient production on a daily basis. Therefore, their actions have a significant impact on the results. If you exclude your operators from the process, they cannot be fully involved in OEE implementation.
This results in reduced communication or insufficient data in some cases. And it eventually affects the OEE score and the potential improvement actions your organisation may wish to take.
What to do: Your company culture defines the success of OEE implementation. And this is closely related to how engaged your operators are in the whole process. So, once you decide to implement OEE tracking, it is crucial to make everyone in your team part of the process. This eventually affects the accuracy of your OEE calculation.
How can you make the process efficient for everyone in your team? Do they need additional help or another tool to get the most out of the OEE system? You need to emphasise their role in keeping the company competitive by improving production. To achieve that, you need to communicate the importance of using OEE software.
The more you emphasize your team’s role in keeping the company competitive, the more they are willing to use the system. When motivated, operators tend to share more about the production process. They insert more information into the system. More information means more accurate data. And it eventually leads you to the desired OEE value and a smart action plan to improve step by step.
The result is increased productivity, along with an increased feeling of commitment, responsibility, and inclusion in the workplace on the operators’ side.
3 – Using standard speed instead of design speed (Nameplate Capacity/Ideal Cycle Time)
When calculating OEE, some organisations tend to use standard speed (historical targets) instead of design speed to gauge their performance. The term, design speed, refers to the production speed, that you can ideally achieve on a production machine. And this, in most cases, is defined by the machine manufacturer.
So, these organisations basically compare their OEE scores with their average (standard) values instead of setting the higher targets which are accepted in their industries. The problem here is that, when your goals are low, your standards become low as well. The result is overlooking the opportunities that can improve the process.
What to do: Your goal should be to structurally shorten the cycle times, thus increasing productivity. For example, process restrictions might justify using standard/nominal speed to avoid the drop in availability. But you need to concentrate on shortening the cycle times and finding ways to solve issues that may arise. This is an excellent opportunity to increase productivity and make the necessary changes.
By shortening the cycle times, one of our clients in the wood processing industry achieved higher speeds than those designated by the machine manufacturers. So, in some industries, you should not take what machine producers give at face value. Instead, you should always pursue the goal of shortening cycle times.
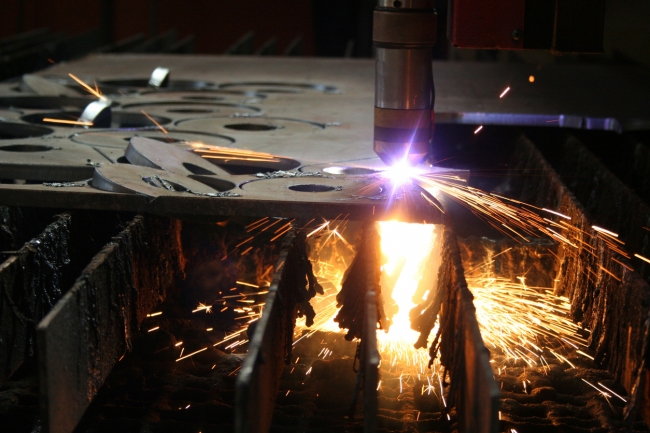
Making mistakes in the OEE calculation can ruin the expected outcome pretty quickly / Picture: Getty/iStock
4 – Insufficient data collection
To calculate OEE, you need to take availability, performance, and quality scores into consideration. Using an erroneous value or omitting of one of these metrics can affect the results significantly.
One of the mistakes in OEE calculation is that in some organisations, operators may not be as engaged in the process as they should be. Or the production department uses standard speed, instead of design speed when calculating OEE. Both situations result in poor quality data. And you cannot fully rely on it to improve your productivity.
Another reason for insufficient data collection is paper-based production monitoring. If you are monitoring your OEE manually, then some of your data might be missing. Or in some cases, operators may not note down all of them. So, whatever is left in their memory after a long working day, actually affects your OEE score.
What to do: To calculate OEE accurately, you need to take the correct values into consideration and set targets. Once you receive the data, you need to evaluate it and identify the problems.
The more you monitor and learn from your production process, the more easily you can adjust your targets based on the data collected. When implementing an OEE system, always keep in mind that data can create a difference only when analysed and acted upon.
For more accurate results, you can implement a cloud-based OEE solution in your organisation. So, you and your team can fully benefit from the reliability of automated data collection. The more you digitise your production process, the more you can monitor and improve it.
5 – Focusing on the OEE score, not the underlying losses
When calculating OEE, companies generally tend to focus only on the OEE score. They ignore the other values, which are the real factors needing to be looked at to unlock opportunities for improvement on the shop floor. They are availability, performance, and quality.
What to do: Having the OEE score presents you with the “big picture” and your overall production performance. However, knowing the availability, performance, and quality values show you the root causes and bottlenecks in the process. Once you know the reasons for the loss, you can come up with solutions to optimise your production.
Instead of focusing on the OEE score, you can take each of the elements in the production process into consideration. Are you losing too much time during changeovers? What is the reason behind the defects? How is the overall performance of your machines? The data will give you the answers.
Looking at OEE as a whole, you can make improvements in availability. Then, you can see how this affects performance and quality. If there is a need to increase performance, you need to observe this in relation to the two other factors. Regardless of the size and industry of your organisation, every decision you make defines the output of your production process.
6 – Comparing the OEE scores of different plants and machines
One of the mistakes in OEE calculation is that organisations compare the OEE scores of different plants and machines with different features and goals. In some cases, companies tend to average over the whole plant. This is when you begin to miss all the details that are actionable —such as the reasons for stops.
What to do: When comparing OEE scores of different plants or machines, you need to take their features into consideration. You should not evaluate a machine producing small batches and another one creating bigger ones in the same context.
Also, the same machines with different maintenance histories and different input material quality levels can produce different outcomes as well.
Regardless of the size or the industry of the company, there is no point having an average OEE score for the entire facility if there are differences in machines. You need to analyse each line or machine according to its own targets and environment.
So, you can only compare OEE scores of machines and plants with the same machinery, the same or similar processes, and which use the same materials. To compare other metrics, data collection should be standardised as much as possible and reasons for stops are one of the most important metrics that you need to take into consideration. In that sense, you need to benchmark stops if configuration settings are standardised, instead of only focusing on the OEE number.
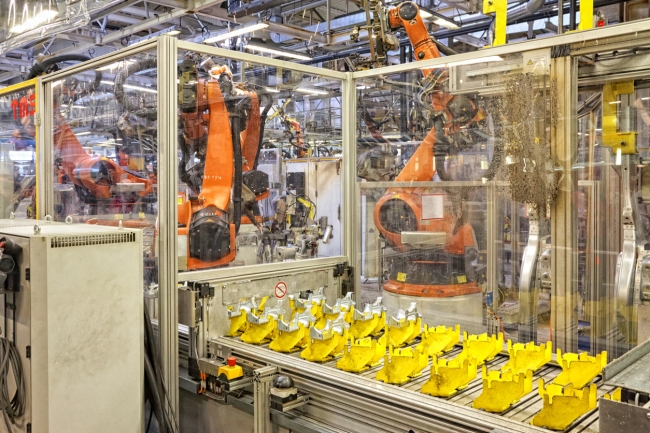
A correct OEE calculation can enable you to receive accurate data regarding production, work on ‘real’ numbers, and come up with the solutions to get the results you want / Picture: Getty/iStock
7 – Not standardising OEE calculation
When you implement OEE in different plants and factories, you need to standardise your efforts to communicate effectively within your organisation.
Some companies fail to centralise their data collection from different plants and machines in one OEE software, which results in decentralisation and communication problems. As a result, factories do not know about each other’s improvements. Besides, managers cannot make responsible decisions as they have different OEE scores coming from various sources.
Ultimately, unlinked, plant by plant OEE tracking results in poor OEE implementation.
What to do: OEE implementation gives the best results when standardised. In multinational businesses with different plants and different departments, you need to have comparable results coming from one source rather than from several places. Once you standardise your OEE monitoring, it becomes easier to monitor, track, and compare the scores, having past numbers as a benchmark.
The ability to standardise OEE significantly benefits your organisation in return. You not only gather a common database of logged and archived information but also enhance communication across plants, factories, and departments.
To learn more about this, please take a look at our article on standardised OEE systems here.
8 – Not taking action on data
You use OEE software, receive real-time data, and analyse it. You have some ideas about what is working and what is not working on your shop floor. On the other hand, unless you come up with solutions to the challenges you identify and then take action accordingly, the data in your reports remains the same.
Briefly, OEE does not improve by itself. Data has an impact only when used and acted upon.
What to do: As a first step, you can analyse the data and pick the easy-to-solve problems which will have a high impact. This creates a feeling of success from the get-go.
Secondly, you should make short daily performance overviews, start to discover the bottlenecks in the process, and come up with solutions. The goal here is to make the process go more smoothly on a daily basis. So, you can track the process more efficiently and gain the ability to predict problems, which you would not achieve by working on one-month reports with a bulk of accumulated numbers.
Production monitoring is a process. Start with small steps, include the whole team, and create significant change on your shop floor by setting well-defined goals.