4 minute read • published in partnership with CKF Systems
Insight: Tooling up for customised robotic automation
The very latest industrial robot technology from global manufacturers provides a plethora of choice to end-users for articulated arm robots, with regard to quality of build, numbers of axis, operational environments, specification, reliability, performance and commercial advantage. Modern robot development has provided the industry with proven, reliable, non-dedicated automation, capable of being re-purposed and re-programmed to meet future demands when necessary.
The decision for robot selection is inherently a primary process prior to committing to the investment in automation of a clients’ process. Of equal importance, however (some may argue, of greater importance), is the interface between the industrial robot and the work object for the successful implementation of robotic automation. The tool interface can take numerous forms dependant on the task to be undertaken.
Proprietary grippers and vacuum pads make up a large part of standard palletising tooling, but there is also an industry requirement for bespoke applications where the use of standardised tooling does not meet the specific needs of customised applications. The correct design and build of the interface between the robot and the workpiece has to be resolved and be dealt with correctly. The right tooling solution will determine that the system as a whole will perform efficiently and that the investment, through the implementation of robotic automation, can be fully realised.
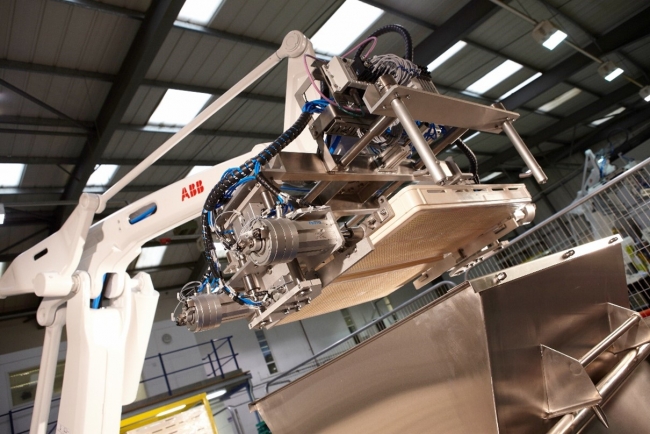
Modern robot development has provided the industry with proven, reliable automation, capable of being re-purposed and re-programmed to meet future demands / Picture: CKF Systems
An example where CKF has designed and supplied a range of special-purpose robot tools is for one of its long-standing confectionery customers. The client approached CKF to develop a robotic automated system for tipping confectionery products into a hopper in readiness for final packaging. The confectionery product was held in open plastic trays, multiple, twin stacked on a plastic pallet.
To meet the specified tray throughputs, CKF undertook a complete design review and whilst the column stacked trays nested well, the CKF team recognised the practical challenges with the presentation of the stacks to the robotic automation. Tray and stack tolerancing, environmental conditions (with the presence of starch), product variants, pick axis datums and provision for stack compression all had to be considered.
The CKF team decided that the tool would have built in, multi-function facilities which provides product presentation, conditioning, de-stacking, tipping and re-stacking capability all in the one tool assembly. Using both linear and rotary pneumatic actuators, the tool is able to position, grip (lower trays), de-nest the full tray, tip and position (lower tray stack) and re-stack the empty tray. The ABB IRB 660 robot provided the load carrying capacity, axis accuracy and velocities required. Via the robot controller, the tool is sequenced and programmed to condition the tray stacks ready for picking two trays at a time and likewise for empty placement. A multiple tip option is made available to the operator to cater for the difference in product variants.
From the delivery and commissioning of the first system, CKF has now supplied the client with six production lines using the same robot automation and tooling philosophy on each line.
CKF Systems has a multi-disciplined engineering team with a wealth of experience in robotic automation able to support its clients in the selection and design of standard and customised tooling applications. The depth of experience spans more than a decade of collaborative customised tooling development, handling products in the food, automotive, pharmaceutical and logistic industries.
Further examples of the customised tooling; designed, built and supplied by the CKF engineering team include:-
• Sack handling grippers for the pharmaceutical industry. Robust in construction, yet integrated and expertly designed into the CKF automated system to ensure safe and damage free handling of heavy but vulnerable plastic and paper bulk sacks
• Case pallet de-topping and re-stacking tools for the frozen food industry, handling chilled cardboard cases and profiled freezer card layer separators using a single custom designed robot tool, with vision guidance
• Case, tray and open tote handling tools, designed for fit, function and compliance within the customers defined products and localised environment i.e restricted height operation where headroom negates the opportunity for standardised tooling, open totes, heavy products and challenging mixes of product palletising formats
Tooling designed for the UK egg-producing industry, providing a suite of specialised tools for robot positioning and loading of shippers, bulkers and cases for the full range of egg case variants, CKF has a wealth of experience and knowledge within the industry. Its engineering resource is extremely capable in providing clients with automated solutions to meet their planned business strategy. System design, manufacture and build are centred around its modern facility in Gloucester which affords the company full technical and commercial control of the projects whilst providing robotic and automated solutions that are perfectly suited to its clients’ unique operational needs.