5 minute read • published in partnership with Barclays
Insight: Will 5G and WiFi-6 help manufacturing’s digital transformation
We are going to see much more about the effect of 5G on manufacturing. Digitalising manufacturing is about capturing more and more data, and 5G – the fifth-generation cellular network – can transmit more of this data more quickly, ideal for uses like conveying huge CAD files. Lee Collinson from Barclays explores how these technologies will support the manufacturing sector.
The government is pushing faster communications; on 27 August, the Department for Digital, Culture, Media and Sport launched a funded project to provide 5G to rural communities to help farming businesses track productivity and provide fast download speeds for home workers, which is a rising demographic.
5G has been trialled by companies involved in the Worcestershire 5G Consortium, and two large manufacturing businesses recorded productivity gains from deploying 5G. Early tests at Worcester Bosch, the boiler manufacturer, showed a one per cent increase in productivity. Manufacturing operations at large companies tend to be super-lean, and one per cent is significant. Worcester Bosch’s engineers have a goal of finding a three per cent productivity gain each year, often achieved through many small, incremental projects. Finding one-third of their target in a single project is therefore a huge benefit that could add up to thousands of pounds. “The productivity gains each year deliver significant savings, which accumulate to tens of millions of small savings over a number of years,” says Carl Arntzen, managing director of Worcester Bosch.
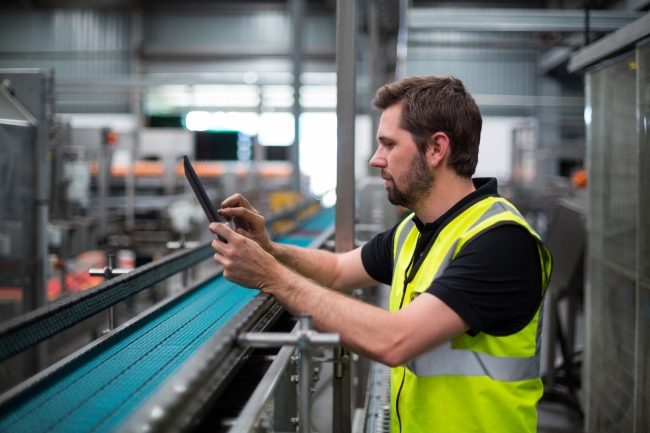
Digitalising manufacturing is about capturing more and more data, and 5G – the fifth-generation cellular network – can transmit more of this data more quickly / Picture: Getty/iStock
Consider that manufacturing contributed £182 billion to the UK economy in 2018, so a one per cent productivity gain could translate to a £1.82 billion increase in GDP.
On the same industrial estate, Yamazaki Mazak also joined the 5G trial and recorded a rise of two per cent productivity in parts of its business. A specific project used the 5G network to connect a video camera on a field engineer’s headset to an operator in an office, helping the field engineer with fault diagnosis and repair. Because the video signal is in real-time the person based at HQ – potentially a more experienced engineer – can explain key steps to the junior colleague “live” with no delay. The trial worked and Mazak is now developing this application for real in the field.
How does 5G provide faster data transfer rates?
5G is a digital cellular network that is divided geographically into cells. All the 5G wireless devices in a cell communicate by radio waves with a local antenna array, over frequency channels that are reused in geographically separated cells. Local antennas are connected to the telephone network and Internet using high bandwidth optical fibre or wireless backhaul connection. The use of local antenna and the choice of frequency channels in local cells partly explain the higher data rates of 5G.
While Worcester Bosch has used a 5G network in a factory this is not the only telecommunications technology being used to enable the “digital factory”.
Mettis Aerospace in Redditch, coincidentally also in Worcestershire, is building a digital factory by trialling WiFi-6 with help from the Wireless Broadband Alliance (WBA). WiFi-6 is the latest generation WiFi, offering the advantages of lower latency – the delay between a packet of data being transmitted and received – high data rates and works well in a multi-device environment. WBA is running WiFi-6 trials in different industry sectors and countries and Mettis is hosting the manufacturing trial in the UK.
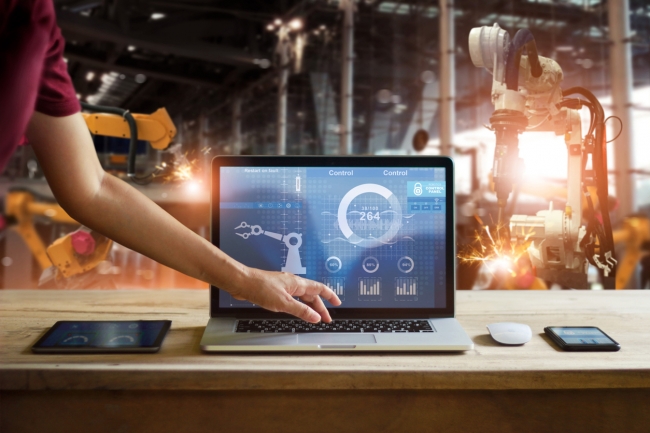
Factories are showing these new telecoms technologies are essential to move into the true “Industry 4.0” mode of manufacturing / Picture: Getty/iStock
Do milliseconds matter in factories?
A question that interests me is that if WiFi-5 is already fast, enabling data from a machine to reach the “operations dashboard” in a few seconds, why do factories need the faster connection of WiFi-6? If machine data can now be transmitted in a few milliseconds, the gain is too fast for the operator or company to react anyway; manufacturing just does not move this fast.
In a share or forex trading situation, however, superfast broadband or WiFi would help because money can be made or lost in milliseconds as trading positions change so fast.
Firstly, WiFi-6 – I am told – is not only about speed. It has an advantage over previous WiFi technology in being able to cope with the thousands of separate communications in a multiple device environment, like a connected factory. Dave Green, Mettis’s IT manager, says the company has about 3,600 assets – machines, devices and computers – over a 28-acre site. The company’s plan to is to connect up the majority of them up so productivity and bottlenecks are viewed in real-time and for better predictive maintenance, detecting faults before they happen from analysing the operational patterns recorded. Without cables and with so many machines linked in a local “Internet of Things”, the wireless network has to cope – WiFi-6 is the most robust platform yet.
Also, several Mettis machines use video feeds to help monitor accurate operations. Its BDP press uses real-time video at several angles to check and control the manipulator arm as it discharges molten metal into the press. “Using a camera with a WiFi-6 connection provides better, faster visibility,” says Sarah Markham at the WBA. “In these environments having hard wire connections can be unsuitable, so doing this with WiFi is an important application. It also needs to have low latency, because without real-time control you risk missing a spill or errors in the process which could result in high costs to Mettis.”
Another feature of WiFi-6 is the use of OFDMA, a form of analysis, to make better use of the communications spectrum. “When you try to use the spectrum and the “availability of the air” to send data packets, this is now much more agile than with former WiFi versions,” says Bruno Tomas, director PMO at the Wireless Broadband Alliance. “Mettis’ grand vision is, after the initial trial, they plan to install at least 20,000 individual sensors across the business to assist with performance monitoring and predictive maintenance in real-time.” WiFi-6, he says, is a better technology to deploy with this future-state in mind, rather than trying to make several existing IoT solutions such as Sigfox or narrowband IoT do what they are not designed specifically for.
Bruno says companies now have a new set of challenges that neither WiFi or cellular have ever addressed. “Mettis Aerospace does not have any wireless technology at all in the factory, so this is about using the technology that best matches their needs when you implement it from the ground up,” he says.
Whether its 5G cellular or WiFi wireless, factories are showing these new telecoms technologies are essential to move into the true “Industry 4.0” mode of manufacturing.