5 minute read • published in partnership with Barclays
Opinion: Automotive sector’s woes masks an electrifying future
While Brexit will pull many headlines and be at the forefront of minds in the automotive industry (and many other industries no doubt), it is definitely worth giving some headspace to the systemic changes affecting the global car industry. Transportation is gradually migrating from IEC (internal combustion engine) power to non-fossil fuel propulsion, of which electrification will be a big part. Lee Collinson from Barclays looks at why this has seismic implications to car manufacturing, affecting components, the supply chain, assembly lines, skills and jobs – over time everything will change to support full or hybrid electric vehicles.
The speed and extent to which this transformation will take place is hotly debated. But now that the UK government has set a legal target of 2040 when all newly manufactured vehicles made here must be hybrid or electric, the clock is ticking and the industry is in a race to build up electric-component infrastructure – some of which, reassuringly, is British.
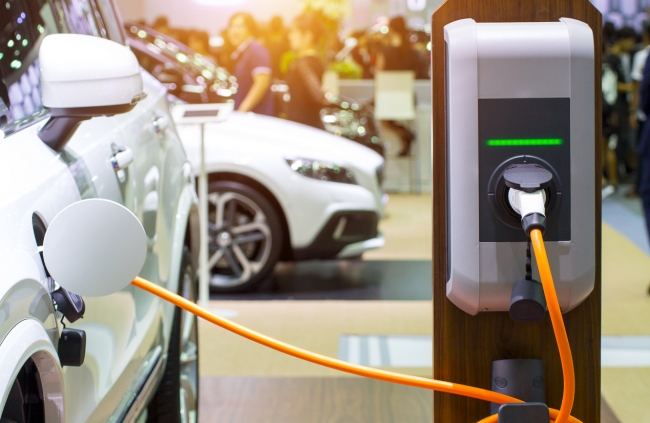
With the migration to electrification, this has seismic implications to car manufacturing, affecting components, the supply chain, assembly lines, skills and jobs / Picture: Getty/iStock
Who’s embracing electric vehicles?
The big car manufacturers in the UK have nearly all made statements that their ranges will include electric models. “Jaguar Land Rover has said that all its engines will have an electric version by 2020 and Nissan will make more electric versions,” said Professor David Greenwood, who leads the Advanced Propulsion Systems team at WMG at the University of Warwick. “BMW is also building the electric mini in Cowley, and Toyota announced it would manufacture a hybrid car for Suzuki in Burnaston with the powertrain made at Deesside.”
Ford’s pathway to electric is less clear and there is uncertainty about whether its UK engine plants will be selected for any electric powertrain conversion. This has encouraged Ford of Britain, and beyond – to include the Automotive Council, Advanced Propulsion Centre and other strategic players – to build a case that the UK is a good place to build electric vehicles.
While Jaguar Land Rover (JLR) has posted bad news this year, including big cuts to its global workforce to save billions in costs, it has some good news too. The enormous Wolverhampton engine plant is being readied to manufacture electric drive units or EDUs, alongside petrol and diesel engines, later this year. The EDUs will be powered by batteries assembled at a brand new JLR Battery Assembly Centre in Hams Hall, Warwickshire.
Why it matters to you – scaling an opportunity
Battery and motor manufacturing development in the UK faces a challenge of scale: the big car OEMs need big tier one suppliers to guarantee battery and component supply and some of the newer, specialist battery companies don’t manufacture at that scale. The low to mid-volume specialist vehicle band is an area where battery companies can prosper, finding customers for the volumes they make. The UK has several such companies like JCB, bus makers Alexander Dennis and Wright Bus, sports car brands like Aston Martina and Lotus and Geely, China’s automaker that makes both diesel and electric London taxis in Coventry. It is an essential market to nurture electrification in the UK. “The low volume automotive makers are important because high volume car companies will bring battery manufacturing in-house, but the low volume space will need tier one suppliers of batteries and motors,” said Prof Greenwood.
What about the opportunity for a very large factory for batteries – not on the scale of Tesla’s Nevada gigafactory, but a facility to supply the global OEMs. “There is an optimum economic size for a mainstream battery plant recognised to be as 9 gigawattt hours,” said David Greenwood. “Such a plant would or should manufacture from 300,000 up to 500,000 units a year. Currently the JLR plant in Hams Hall might be expected to produce 40,000 units so we don’t have this volume. If such a plant were built in the UK it would be able to supply a BMW or Nissan.”
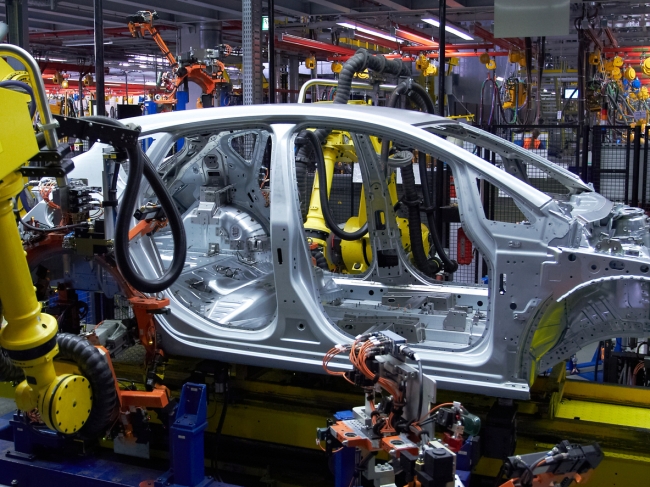
Now that the UK government has set a legal target of 2040 when all newly manufactured vehicles made here must be hybrid or electric, the clock is ticking / Picture: Getty/iStock
It would be great to see a global company invest in the UK with a 9GW/hour factory but, like other decisions about macro investment on manufacturing, it will depend on the skills and the coordination of investment and organisations.
As with JLR’s decision to build a factory in Slovakia, the main competition for the UK for a global battery company is likely to be Eastern Europe, which has tax breaks, enterprise zones with no rates, low wages and other fiscal incentives. How does the UK compete? The level and type of incentivisation here is different, and some state money might be available via programmes like the Advanced Propulsion Centre, which helped finance the HyperBat project, but here is more about economic stability, a skilled workforce, low trade barriers and access to expertise.
Leading the charge
Battery suppliers, and more specifically electric powertrain component suppliers, in Britain including among others Delta Motorsport, Hyperdrive – that is working with Nissan on electric motors – McLaren Applied Technologies and HyperBat. The last one, a joint venture between Unipart and Williams Advanced Engineering, will be the UK’s largest independent vehicle battery manufacturer and is due to open soon. And just this week (8 April) FTSE-250 listed engineering consultancy Ricardo it is to build a new electric car battery manufacturing plant in the UK, with Sheffield, West Sussex and South Wales among the potential locations. So much battery manufacturing construction is a very positive sign for the potential growth of the electric car industry and also a welcome fillip when other auto news is more circumspect.
Looking at motors outside of automotive
With so much focus on batteries, don’t forget there are motors – more accurately known as electric machines – inverters and other components that can be upscaled to give the auto sector a jolt. With electric machines, the new Stephenson Challenge is a scheme to incentivise companies to create a supply chain of parts for advanced motor manufacture, similar to the Faraday Challenge for batteries. And the research council, UKRI, announced in 2018 a new £10 million future manufacturing hub for researching the manufacture of electric machines. This combines the brainpower of specialists at the universities of Sheffield, Newcastle and Strathclyde, to design new electrical machines with improved performance for applications like offshore wind power, rail and automotive.
On the face of it, the UK is really well placed to “go electric” but there is no time to be complacent and we will need more investment in R&D, the right skills and facilities to secure a big domestic and international manufacturing industry for electric and hybrid transportation.