5 minute read • published in partnership with Barclays
Opinion: Supply chains disrupted but cost is still king
The pandemic in 2020 has naturally sparked a big conversation about supply chains. Supply chains for complex and costly products are always in flux but the changes are frequently small – radical changes to traditional supply chains, such as for the automotive industry, are disruptive and expensive (although with electrification this is what the auto industry will face over the next 20-years as a phased transformation). Lee Collinson from Barclays looks at how manufacturers have had to adapt their supply chains to meet the demands of Covid-19.
Production of essential goods never stopped, and many ramped up. We know all about toilet roll. Factories in busy sectors like dairy, flour mills and breakfast cereals had to quickly cope with higher demand, driven by higher domestic food consumption with a reduced workforce as factories observed safe working practices and some employees were self-isolated. In March the National Association of British and Irish Millers said the industry was “working round the clock”, milling flour 24 hours a day, seven days a week to double production – but was still struggling to meet demand. It attributed the rise in home baking.
But now there is a more urgent conversation in the food industry about food security, driven by supply chain disruption caused by Covid-19 and also labour shortages in both picking/ harvesting and food processing. Big commodity crop exporting countries like Kazakhstan have suspended exports. The Institute for Manufacturing says the UK relies on 50% of its produce from imports and asks should the proportion we produce ourselves increase?
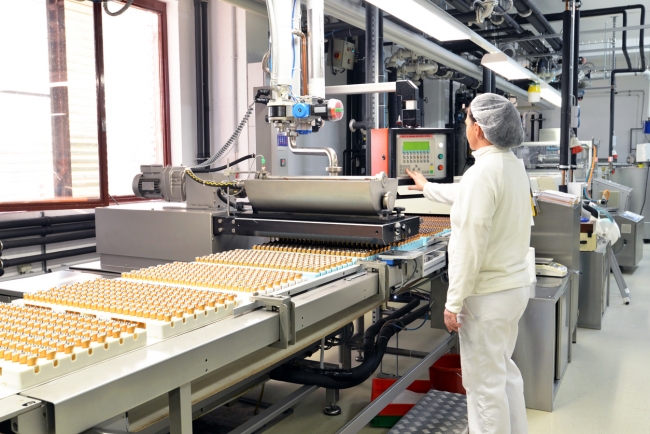
The pandemic has shown that it is important for the UK to have domestically resilient supply chains for products and services / Picture: Getty/iStock
The flexibility of big companies is being tested to the limit by Covid-19. The Ventilator Challenge mobilised a group of prime companies to make thousands of Penlon and Smiths Medical ventilators. Companies like Airbus, GKN and Renishaw had to “pivot”, at short notice, to make new components with brand new tooling and processes hitherto untested in their factories and in record time. The demand for these ventilators will soon – we hope – decrease to a trickle, and the Ventilator Challenge teams will return to what they manufactured before whilst staying on stand-by.
What does this prove for UK supply chains? It showed that big companies, often seen as inert and slow, can respond very quickly if they are forced to, they can shelve conflicts, collaborate with others smoothly, reconfigure millions of pounds worth of plant and tooling and pivot quickly. This bodes well for the future of manufacturing – the ventilator response will be seen as a test case for other rapid response manufacturing capability and industry collaboration.
And it’s not only ventilators.
Chemical giant INEOS converted a factory near Middlesbrough in 10-days to manufacture hand sanitiser, with capacity to make one million bottles a month. Outdoor clothing brand Barbour changed its lines to produce from 1,000 to 1,500 disposable gowns a day for local NHS trusts. Defence equipment manufacturer Hard Shell installed surgical mask making machines in a new factory in Cardiff to produce up to one million fluid resistant face masks per day and Ford in Dagenham also bought machines to make their own PPE gear to avoid being a drain on PPE for frontline workers.
Add the numerous stories of SMEs pivoting to make PPE, motors, switches, springs, seals, cups, vaccine testing kits, swabs, sharps buckets and more – often working double shifts and weekends – proves how responsive companies can be when circumstances demand.
Managers of complex supply chains, like Deloitte, have observed different behaviours in response to covid. “Depending where you operate within an industry and a supply chain, we have seen different behaviours – from supporting manufacturers to diverting manufacturing capability to other countries, to simple renegotiating practices,” Kristian Park, Global Leader of Extended Enterprise Risk Management at Deloitte told Barclays.
“Deloitte’s clients are looking at three things. Firstly, data to assess what’s happening with distribution, logistics, workforces and commodity rates, and how these will affect their parts portfolios. Secondly, directing operations away from the hardest hit areas to maintain supply. But, gathered more from on the ground intelligence, we see a compassionate response, how companies support other manufacturers that have been hardest hit, e.g. giving them more leeway on business terms.”
“The most interesting thing is that, as time evolves, supplier conversations are moving from the compassionate “let’s see what happens” response to more hard-nosed business dealings, more active renegotiation”, said Park.
Covid-19 is showing us that it is important for the UK to have domestically resilient supply chains for products and services that are critical to life. We have mentioned food security. Supply chain experts at University of Warwick say that one of the reasons why UK food supply chains have been so effective at maintaining supply, is that much of their food production is based in the UK – although many would say domestic food production must increase for better food security, and exports. Professor Janet Godsell at Warwick says, “the UK needs to strategically review the products that are critical to life and ensure that there is the capability to produce these domestically, with the ability to ramp up volume if required”.
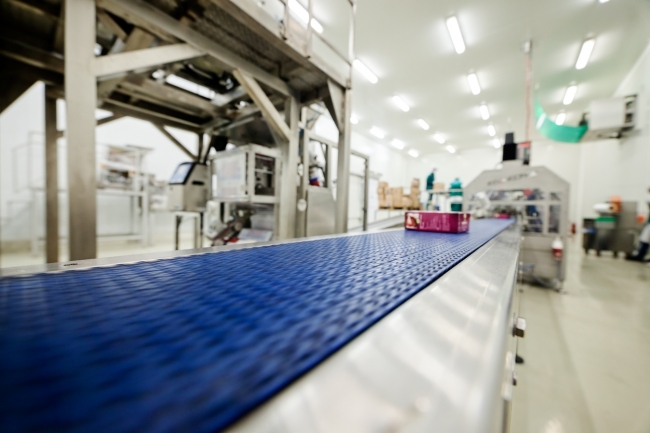
Covid-19 is giving the UK a unique opportunity to change what we make, where we source from, consider the environment more, make locally and accelerate the use of digital technology / Picture: Getty/iStock
Britain has typically focused on manufacturing components and final products, while other countries like Germany and Japan focus on the manufacture of the equipment to make products. “As we move into the post-Covid-19 era, the UK needs to start investing in a programme of research and development to support the next generation of manufacturing production technologies and identify opportunities for new emerging technologies where we may be able to ‘leap frog’ the competition, where a longer-term investment plan is critical to long term success,” Janet Godsell says.
The pandemic is giving us some time to review what we could do more of, as the economy adapts. For example, with aerospace in crisis, will aerospace primes and suppliers pivot more quickly to a new propulsion paradigm based on hybrid electric, and hybrid hydrogen, power? Automotive is rapidly switching to electric and Covid-19, by reducing sales of IE engine vehicles, will accelerate that. On May 19th two UK start-ups announced plans to invest up to £4bn in building a battery “gigafactory”, comparable to the Tesla plant in Nevada, USA.
There is also much talk now about re-building industries and supply chains with a much more consideration for the environment. There could be a rise in local manufacturing, closer to the end-market. This new system, says Prof. Steve Evans at the IfM Cambridge, needs flexible factories and “must be resilient to ever-increasing frequency of shocks to supply / demand /quality, so the manufacturing system will use information systems to help manage that variation. Today we manage it through very lengthy supply chains that consistently deliver consistent quality. Imagine a factory that senses what is being wasted around it (local farmers’ waste, other local factories’ waste, supermarket waste, construction waste), and dynamically calculates that it could make shampoo from that waste next Thursday. It would need to get agreements in place to obtain the waste, organise the logistics, re-configure the factory, and find a market…”
While Covid-19 is impacting GDP, it is giving the UK a unique opportunity to change what we make, where we source from, consider the environment more, make locally and accelerate the use of digital technology.