5 minute read • published in partnership with Evocon
The benefits of a standardised OEE system
The primary goal of implementing an OEE system, both locally and globally, is to be able to measure the performance of your processes effectively. And the result, of a standardised OEE system, is that teams can benchmark themselves against past baselines and share best practices. Evocon looks at how one company went from an unlinked, plant by plant OEE tracking software, to a centrally run standardised OEE system, and what they achieved in the process.
The company utilised many types of machines and processes varied from plant to plant. Everything from injection moulding equipment, to continuous extrusion processes, thermoforming, and discrete die cutting activities happened globally. This meant that more than a hundred machines operated at every moment of the day.
Before the change, OEE tracking had been implemented in seven of the ten locations. And in each instance, the plants used the same OEE software to track and measure production performance, but they were not interconnected. Furthermore, since the implementation was decentralised, every site did the installation on their own and how they best saw fit.
As a result, at each local system, optimised versions developed over time, the systems across the factories lacked standardisation, and the teams used OEE efficiency metrics differently.
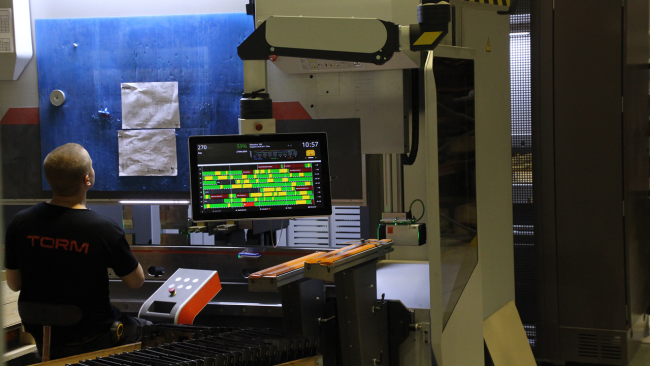
The primary goal of implementing an OEE system within a manufacturing facility is to be able to measure the performance of operations and processes effectively / Picture: Evocon
The challenge
The need to understand OEE was important, especially given the growth potential for the group. And many questions about actual capacity were being asked. The already installed OEE systems at each site helped, but the local improvements did not have a significant effect on the global business.
The other problem was that the information that the corporate team had from local factories showed variances to the possible improvements. For example, one of company’s plant reduced its machine downtime by installing a simple changeover mechanism. This reduced process downtime by 30%. Two of the other sites had the same equipment, running similar products. But no one from the other two factories knew about the improvements.
A few months passed, and on a visit through the plants, a corporate manager noticed gaps in OEE on the same products in three different workshops. He quickly realised that this was because the changeover fix had not been introduced to the other sites.
The main reason for this falling through the cracks was that the OEE system was not standardised and no data was shared between different factories. So plants did not know how their sister plants were doing.
It is an excellent example of how the individual application of OEE creates a system where people are not aware of the challenges and improvements other plants are making on daily basis. And one factory manager or the other will miss simple chances to improve.
Time to change: standardise OEE
After the incident, the plastics company leadership team realised that one of the most critical benefits of having one standardised OEE system is the ability to gather a common database of logged, archived information. And that this information must be available to every site connected to the system.
The company decided to standardise the implementations across all facilities. A common process procedure that looked at OEE across all machines in each plant was also a part of the new process.
Once installed, they benchmarked several processes and created standard run levels. Even in places with a highly manual process, the business designed new baselines to start.
Each measured process got divided into groups and rolled up to one overall OEE metric. The rolled up OEE at the start of the project ran at about 20% to 30%. The business agreed a positive upwards trend would be their first-year goal.
After two months, before the complete implementation, the company started seeing returns on its investment. As each factory (and each production line) came online, the sister plants could look into each facility. Each day they were able to observe and comment on the progress.
Year one highlights
After just one year the company experienced more benefits than anyone could hope for:
• Many people had been part of the expansion into the Asia regions. But now, for the first time in several years, they could see the performance (in real time). As a result, the communication around machines, material, and people was very active, and improvements occurred daily.
• New visibility to OEE globally gave leaders a much better understanding of the results for comparing profits in each plant.
• They improved the yearly task of capital expenditures. Which was possible because now the teams used OEE performance as a means to check their spending against the highest needs of the business.
• The team developed a Pareto of best processes. And an issues list of the highest priority process problems became the bias for action.
• Additionally, the company created a central top-down support system. The team in charge of this kept an eye on the highest priority issues. And as a result, they were able to get faster gains from continuous improvement teams.
• Prior to the standardised OEE, each factory reported quality, cost and delivery (QCD) monthly with explanations for ups and downs of these metrics. Now with the new system, the effects on QCD were more easily understood and communicated.
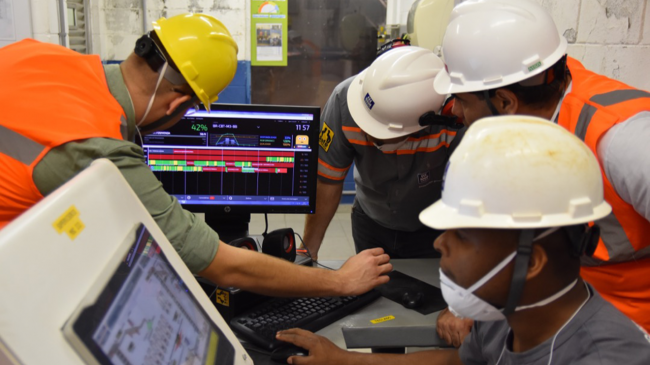
The ability to influence processes, separated by geography, has never been easier than with a central real-time OEE tracking software / Picture: Evocon
Year one savings
Not only did the company experience numerous benefits but as a result, they increased their savings in many ways:
• All ten sites have realised at least a 4% reduction to cost of goods sold since the centralized OEE went in. And they expect to further remove waste by monitoring OEE.
• Quality yield went up from 90% (global average) to 95%. The Asia sites have all reduced the cost of poor quality by 35%. The next goal is to eliminate all recurring nonconformances. And they believe this is possible because of the open communication between all plants.
• Machine availability went from 50% (average) to 75% in the first six months, and they now share downtime reasons and fixes. This change alone accounted for much of the initial savings.
• Performance efficiencies were 60% to 99% in some cases. The global average of 75% inspired leadership to input a better policy for the use of equipment. The impact on global capacity allowed the team to create a new approach to capital expenditures.
• The end of year global average for OEE was at 70%, up from 30% at the start. And the plant teams now have more consistent metrics.
• OEE centralisation also influenced the empowerment of the operations teams to own the entire operation, not just the plant they work in.
A universal language in the digital factory
A close look at OEE implementations in single plants of a multinational organisation will see similar opportunities to the case study above. For corporations considering using OEE for the first time, the plant-by-plant pilot test is not the best approach.
Sure, pilot testing OEE on a piece of equipment is a good way to test how a certain OEE tracking software works. That is also why Evocon has a free trial program for all new companies. But afterwards, you need to coordinate the implementation centrally. The decentralised tactic is doomed to cost more and leave much of the payback on the shop floor. And all the common pitfalls described above are going to happen.
Masaaki Imai, the famous Kaizen improvement guru, said, “continuous improvement is everyone, everywhere, everyday improvement.” To achieve the ideal state of continuous improvement, we must change our ways. To have all personnel (in all plants) focus on the right things, and do this every day, will be difficult or impossible without a centralised system of performance measurement. But a standardised OEE system provides the means to achieve this.
A well run OEE system data helps formulate the right goals for the entire operations team. Everybody, everywhere, working every day on the same objective to improve OEE globally. An eloquent solution to one of the biggest challenges a company will face.
Ask yourself a simple question: “Are all your people in each plant globally, working together on a common goal?”
One OEE system, one standard approach
The ability to influence processes, separated by geography, has never been easier than with a central real-time OEE tracking software. It is imperative to avoid the urge to install single systems of OEE in different plants. As this will cause delays in gaining the benefits of implementation.